Cet article présente la réalisation d'une table de bridage (parfois appelée marbre) pour la soudure et le travail du métal. Elle est électrifiée avec des prises 16A et 32A, équipée d'un bac récupérateur des déchets et d'un plateau relevable motorisé.
Sommaire de l'article (cliquez pour replier le sommaire)
État des lieux
Pour celles et ceux qui ont pris le temps de lire mon histoire, vous savez que je suis contraint de fabriquer une quantité importante de pièces en métal parfois de grandes dimensions (toutes proportions gardées), notamment plus ou moins 80 mètres linéaires de garde corps extérieurs et bien d'autres encore (pergola, carport, verrière, portail, etc).
Il n'était donc ni question ni envisageable de fabriquer ça à quatre pattes par terre ou sur des tréteaux. Pour travailler correctement, pour préserver ma santé, pour être efficace et travailler en sécurité, j'avais besoin d'une table de bridage adaptée à la soudure et à toutes les opérations courantes dans le travail du métal (meulage, découpe plasma, etc).
Qu'est-ce qu'une table de bridage ?
Si vous êtes arrivé(e) sur cette page, je pense que vous savez probablement ce qu'est une table de bridage et quel est son usage. Je vais néanmoins rappeler rapidement de quoi il s'agit pour celles et ceux qui se poseraient la question et seraient arrivés là par hasard 🙂
Une table de bridage est un équipement utilisé pour maintenir les pièces pendant le processus de soudage à l'aide de serre-joints à tête fraisée ou d'autres accessoires (équerres aimantées, bench dog, etc). Ce maintien est crucial pour garantir la qualité des soudures et la sécurité du soudeur. Brider les pièces permet de maintenir leur alignement précis pour éviter leur déplacement mais également de limiter au maximum les déformations liées à la chaleur.
Une table de bridage offre une surface de référence plane nécessaire pour obtenir des réalisations d'équerre qui ne "boitent" pas lors de la réalisation de piètements par exemple.
Il peut-être utile de rappeler qu'une table de bridage doit être maintenue propre pour éviter toute "contamination" des soudures. Il est recommandé de nettoyer régulièrement la table de bridage et ses accessoires pour éliminer les résidus qui peuvent polluer le bain de fusion.
Le cahier des charges
Suite à l'inventaire de mes besoins réalisé en essayant d'anticiper au maximum mes usages futurs, le cahier des charges était le suivant :
- Surface de travail d'environ 200 x 100 cm (hauteur 93,5 cm sur roulettes, mais je suis grand) ;
- Table de bridage modulable avec rallonges (pas encore installées à ce stade), plieuse à tôle, etc ;
- Avoir le maximum de rangements pour conserver le plus possible d'outils et machines à portée de main (notamment les disqueuses, les outils de mesure ou de bridage) ;
- Avoir une table de bridage mobile, sur roulettes et calable de niveau avec des pieds machine ;
- Bien entendu un plateau en tôle percée à intervalles réguliers diamètre 16 mm pour pouvoir utiliser les outils standards de bridage ;
- Avoir un bac collecteur sous la tôle perforée pour éviter que tous les déchets (limaille, laitier, etc) ne tombent sur les outils stockés en dessous ;
- Avoir le plateau inclinable et vu son poids motorisé, pour pouvoir nettoyer le bac collecteur et travailler au besoin sur une surface oblique ;
- Table de bridage électrifiée sur 2 "réseaux" distincts (monophasés, pas de triphasé à disposition) pour gagner de la puissance disponible, avec plusieurs prises 16A et 32A positionnées de chaque côté afin de pouvoir brancher (et laisser branchés) le maximum d'outils ;
C'est donc avec un nombre relativement élevé de contraintes que je me suis lancé dans ce projet qui m'aura tout de même occupé pas loin d'un mois. Je n'ai malheureusement à l'époque pas filmé les étapes de fabrication de cet objet par manque de temps, il y avait urgence à avancer et le projet IronWood n'était pas encore concret.
Heureusement, j'avais fait des photos, outre le fait de pouvoir en parler, ça permet de se souvenir comment certains assemblages difficilement visibles aujourd'hui sont réalisés.
L'objectif de cet article, en raison du manque de visuels, n'est pas de détailler chaque étape de fabrication mais plutôt de présenter de façon globale la méthode de conception, ce qui peut donner des idées si vous souhaitez réaliser quelque chose de similaire (et peut-être même vous montrer ce qu'il ne faut pas faire 😂).
Provenance des matériaux
Je ne suis pas parti d'une feuille blanche mais d'une table de soudure existante pour plusieurs raisons. J'ai acheté d'occasion ce qui ressemblait plus à un établi métallique en piteux état qu'à une table de bridage. Il était bancal et mal soudé, la tôle était trop fine pour être utilisée seule (6 mm) et il avait plein d'autres défauts.
Mais il avait tout de même quelques qualités... Il disposait déjà d'une structure métallique (que j'ai en partie démonté et refait) avec sa tôle d'acier et je ne l'ai pas payé cher, moins cher que si j'avais dû acheter neufs ces fournitures. En procédant ainsi j'ai donc gagné du temps et de l'argent.
Je n'ai malheureusement pas pensé à faire des photos lors de l'achat, mais ce n'était pas jojo, c'était une simple structure tubulaire sans rangements avec une tôle boulonnée aux quatre coins. J'ai retourné la tôle lorsque je l'ai remontée avant de la percer car son état de surface n'était pas terrible.
Je n'ai pas de plans disponibles à vous proposer étant donné que je suis parti de quelque chose d'existant, j'ai fonctionné avec des croquis, des schémas et des notes.
Déroulement de la fabrication
Après avoir remis d'aplomb la structure de la table et rajouté des renforts et des traverses à plusieurs niveaux (pour installer les rangements et le moteur avec son bras de levier), j'ai installé des tôles pliées en fond pour pouvoir ranger du matériel.
Puis j'ai inséré au dessus un rayonnage plus petit en tôle galvanisée pour permettre d'y poser du petit matériel et protéger l'installation électrique des chocs et arrachements par le dessous.
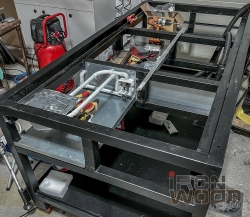
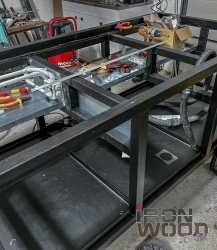
J'ai également fixé des tubes longitudinaux de part et d'autre pour y glisser les coulisses des futures rallonges et pouvoir positionner dessus le bac de récupération des déchets.
Le plateau inclinable
Ensuite, j'ai fabriqué un cadre en cornière épaisse de 60x60 mm fixé à l'aide de trois grosses charnières soudées. il vient en recouvrement de la structure tubulaire, les angles sont faits avec des coupes à 45°.
Viennent ensuite des traverses en acier plat de 50x10 mm pour rigidifier l'ensemble.
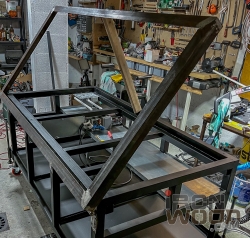
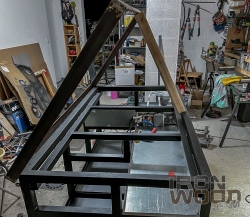
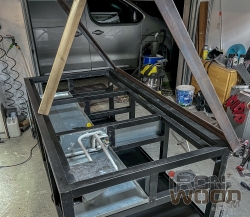
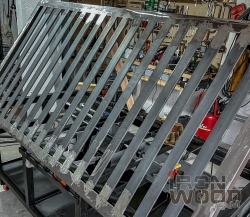
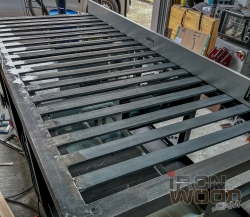
La fonction des traverses n'est pas seulement de rigidifier le plateau de la table de bridage, ça ne serait pas suffisant seules sans la tôle. La tôle de 6 mm qui n'est pas assez épaisse sera perforée Ø 16 mm tous les 10 cm. Les traverses ont été positionnées pour toujours se trouver à l'aplomb de chaque trou qui sera effectué dans la tôle, afin que ces derniers aient une profondeur non pas de 6 mm (insuffisant pour clamper certains outils de maintien) mais de 16 mm.
L'achat d'une tôle neuve de 20 mm d'épaisseur est relativement onéreux et celle-ci serait très lourde et complexe à transporter. J'étais seul pour manipuler l'ensemble et c'était déjà limite. Voilà comment j'ai contourné certaines limitations, ce n'est pas idéal bien entendu, mais ça m'a permit d'arriver à mon objectif à moindre frais.
Et vous, comment vous auriez fait à ma place ? Dites le moi en commentaires si vous avez 5 minutes.
Mécanisme et moteur de levage du plateau
Vient ensuite l'étape de la réalisation du mécanisme de levage du plateau puis l'installation du moteur.
Alors je ne vais pas vous mentir, je ne suis pas ingénieur et je ne sais pas calculer le dimensionnement du bras de levier nécessaire pour faire la jonction mécanique entre le moteur et le plateau. Mon questionnement n'était pas sur sa résistance mais sur ses dimensions pour lever le plateau à la hauteur souhaitée sans que le moteur ne force trop, en tenant compte du débattement limité du vérin.
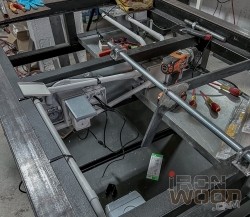
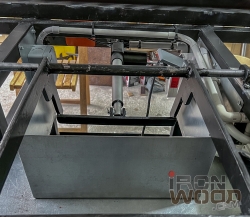
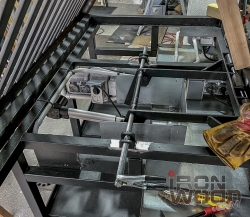
Lorsque l'on n'est pas en capacité de faire certains calculs, il reste la ruse et la méthode empirique. J'avais en tête le design souhaité et j'ai donc commencé par fixer provisoirement le moteur. J'ai ensuite réalisé des maquettes de bras de levier en bois pour faire des essais avec le moteur. J'ai ainsi pu estimer le positionnement avant/arrière du bras de levier, les bonnes longueurs de chaque bras et l'angle adéquat pour arriver à l'inclinaison souhaitée pour le plateau.
Le débattement du vérin étant limité (380-610 mm), il fallait amplifier le mouvement car le placer à la verticale sous le plateau avec une poussée directe aurait été parfaitement insuffisant, d'où le choix d'un bras de levier angulaire. Je n'avais aucun doute après mes essais sur l'angle final de levage du plateau mais j'avoue que j'ai peut-être eu un peu de chance sur ce coup là pour trouver les bonnes sections de chaque côté de l'angle qui engendrent une force de poussée supportable pour le moteur, d'autant plus que je ne connaissais pas le poids final réel de l'ensemble du plateau avec les traverses, le cadre et la tôle de revêtement.
J'ai utilisé un moteur (je cite) de "tables élévatrices et fauteuils de massage" qui a une capacité de poussée de 6000 Newton, soit environ 610 kg. C'est une chinoiserie payée 45 euros qui fonctionne très bien pour l'instant et ne semble pas trop forcer. Pour le bras de levier, je ne me suis pas contenté d'un simple bras qui n'aurait pas été assez rigide et sans redondance en cas de faiblesse. J'ai donc opté pour un double bras de levier dont les bras sont reliés par un tube dans lequel traverse la tige filetée de 20 mm qui sert d'axe.
Cette solution présente plusieurs avantages :
- Elle contribue à renforcer l'axe du bras de levier avec une surface d'appuis plus importante. Prisonnier dans son tube receveur, il ne peut donc pas cintrer sur une partie non négligeable de sa longueur ;
- Elle permet de rigidifier latéralement l'ensemble et de ne solliciter le vérin du moteur que dans son axe de déploiement, sans risque de le tordre ;
- Elle permet de réduire l'espacement entre les points de poussée et les points d'ancrage de l'axe sur les traverses de la structure, relativement espacées pour diverses raisons de conception ;
- Elle permet en bout de bras de levier qui a une certaine largeur d'installer le mécanisme de liaison entre le bras et le plateau, que je décris ci-après.
Très honnêtement, j'ai un peu galéré si j'avais su dans quoi je m'embarquais avant de le faire, et bien je ne l'aurais peut-être pas fait 😂
En tout cas, ça fonctionne parfaitement, je suis très content du résultat et c'est extrêmement pratique. En revanche, il ne faut jamais mettre aucune partie de son corps entre le plateau relevé et les traverses de la table car si le moteur ou le bras de levier venaient à céder, même un bras serait coupé net et sans appel 😱 J'y reviendrai un peu plus loin.
Installation du bac collecteur et liaison avec le plateau
Une fois que toute la partie sous-jacente est terminée (électricité, tôles de protection et de rangement, installation du moteur et du bras de levier, etc), il reste à découper au plasma et à mettre en place le bac de récupération des déchets qui protège le matériel stocké en dessous.
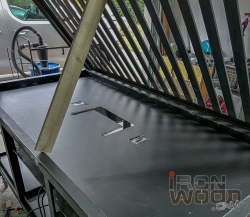
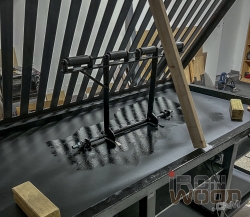
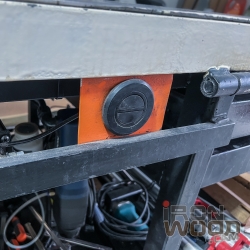
Le soulèvement du plateau via la poussée du bras de levier entraine un glissement de ce dernier contre les traverses inférieures du plateau (photo du milieu). Il n'est donc pas possible de solidariser le bras de levier avec le plateau en point fixe.
La solution que j'ai trouvé pour palier à ce problème est d'utiliser des galets de type transpalette qui supportent individuellement bien plus que le poids du plateau complet. Ils sont en nylon polyamide, montés sur roulements à billes avec une durée de vie quasi infinie pour cet usage vu la fréquence d'utilisation, c'est silencieux et ça fonctionne très bien.
Les galets en nylon permettent également de répartir les appuis sous le plateau. C'est peu onéreux, efficace et relativement simple de conception, même si je me suis pas mal fait suer pour passer la tige filetée et glisser les écrous de part et d'autre des galets.
Avec le recul, je ne vois toujours pas de meilleures options même s'il en existe certainement.
Je vous épargne les étapes de peinture du cadre et des traverses, j'ai fait ça un peu comme un cochon (ça peut-être assez long pour faire du super boulot) avec de la peinture Hammerite métal. J'ai seulement pris soin de dégraisser le support et ensuite j'ai badigeonné au pinceau, à l'ancienne 😂. De toute façon, entre les frottements, les étincelles, les coups de marteau, etc, inutile de faire une peinture qualité carrosserie, il en faut simplement pour protéger un minimum.
Si quelqu'un a perdu sa mère, ce n'est pas là qu'il ira la chercher 🙂
Fixation, traçage et perçage de la tôle
Il est maintenant temps de fixer, tracer et percer la tôle sur le plateau de la table. Je ne vous cache pas que c'est une opération fastidieuse et chronophage, d'autant plus qu'on approche de la fin du projet et qu'à ce stade, j'avais vraiment envie de passer à autre chose...
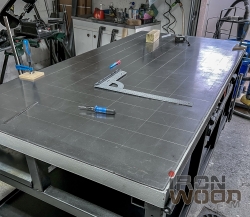
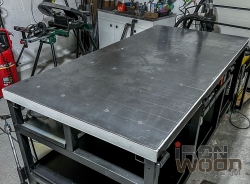
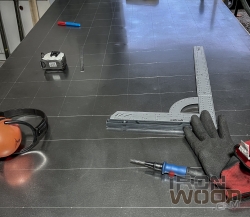
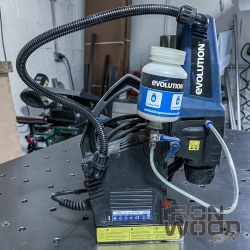
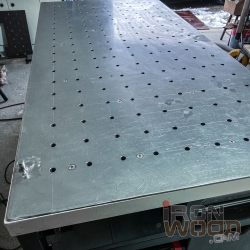
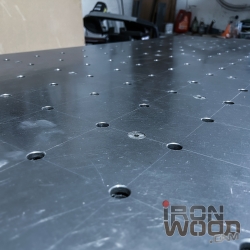
La tôle de 6 mm est vissée sur les traverses avec un espacement jugé suffisant, après que j'ai percé et taraudé l'ensemble (taraudage machine). Le perçage de trous dans ces quantités et épaisseurs se fait avec une perceuse magnétique. Le modèle que j'utilise propose un excellent rapport qualité prix pour un usage occasionnel. Elle utilise des fraises à carotter HSS à emmanchement weldon avec un éjecteur de carotte qui sert également de pointe de centrage avant de commencer le perçage.
Elle possède un réservoir de lubrifiant qui diffuse dans la carotte dans lequel je mets un lubrifiant à diluer à 10%. Acheté en bidons de 2 litres, ça laisse déjà de quoi voir venir et c'est beaucoup moins onéreux que de l'huile de coupe classique.
Alors c'est un investissement de départ certes, qui vient s'ajouter au coût de fabrication de la table, mais vous l'aurez ensuite pour de nombreuses années et c'est autre chose qu'une perceuse à colonne avec laquelle il serait difficile voir impossible de réaliser ce type de perçages en "gros" diamètre sur de telles surfaces.
Les rangements supplémentaires
En plus des bacs en tôle pliée qui permettent de ranger une multitude de gros outils (poste à souder, découpeur plasma, perceuse magnétique, suspension des meuleuses, etc), j'ai rajouté 4 tiroirs charges lourdes pour y ranger les outils de tracé et de mesure, les accessoires de bridage et tout ce que j'ai besoin de garder à portée de main.
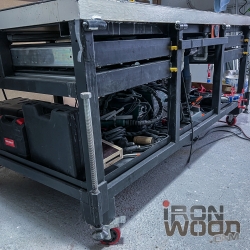
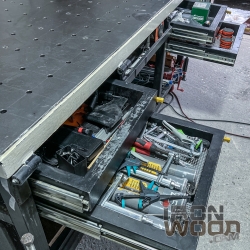
Pour les réaliser, j'ai utilisé des poteaux de panneaux de signalisation routière qui avaient été abandonnés sur mon chantier par les ouvriers qui avaient dû les piquer je ne sais où et pour une raison qui m'échappe... Positionnés sur la tranche avec quatre coupes à 45°, ça fait des cadres de tiroirs nickels et gratuits. D'autant plus que pour faire 4 grands tiroirs, il faut mine de rien une certaine longueur de tube acier.
Attention si vous soudez ce genre de ferraille, c'est de l'acier galva et même si vous le décapez avec la meuleuse, ça produit des fumées extrêmement toxique quand vous soudez. Pour ma part, comme les cordons de chaque face sont courts, je les ai soudé en apnée toutes portes ouvertes même si je portais un masque. J'ai le projet de réaliser une aspiration à fumée avec plus de 2000 m³ de débit d'aspiration mais je n'ai pas encore eu le temps de m'en occuper.
Pour le fond des tiroirs, j'ai simplement utilisé de la tôle perforée de récupération pour ne pas qu'ils se remplissent de limaille, viséee dans le cadre avec de simples vis autoforeuses et c'est impeccable.
La sécurité de l'ensemble
Lorsqu'on se lance dans la construction d'un outil de ce genre, il faut prendre quelques précautions.
Risque électrique et résistance
La première avec une structure métallique qui comporte des câblages électrique est de parfaitement protéger les câbles (tube IRL protégés par de la tôle), en raison de l'abrasion et de la chaleur. Ensuite, il est IMPÉRATIF de bien mettre l'ensemble à la terre, des courants de forte puissance transitent au sein de la structure et on branche dessus la pince de masse du poste à souder par exemple.
Il faut également veiller à réaliser une structure suffisamment solide pour supporter le poids de l'ensemble, mais également et surtout le poids de tout ce qui pourra être posé dessus, additionné de votre propre poids si vous avez besoin de vous mettre debout dessus pour travailler une pièce en hauteur.
Attention donc au choix des roulettes et à leur fixation, les miennes sont boulonnées dans des platines taraudées de 10mm d'épaisseur avec 4 points de fixation chacune. Dans ma configuration elles suffisent mais si j'avais installé une tôle de 20 mm d'épaisseur, j'aurais sans doute été obligé de passer sur un modèle de roulettes industrielles beaucoup plus chères.
Enfin, et c'est spécifique à la table que j'ai fabriqué, il faut sécuriser le plateau lorsqu'il est relevé.
Les jambes de force
J'ai prévu à cet effet deux jambes de force (des sortes d'étais ou de chandelles) pour sécuriser le plateau lorsqu'il est relevé. Elles sont en appuis oblique sur les traverses situées sous le bac collecteur de déchet et une cornière à 90° vient recevoir la cornière du plateau inclinable qui s'emboite. Elles ne peuvent donc pas glisser et les "pinces" de ces étais sont fixées sur leur montant perforé avec des tiges filetées de 12mm (travail en cisaillement uniquement).
Je règle donc mes jambes de force à la hauteur souhaitée, je commence à lever le plateau, lorsqu'il est monté suffisamment, je place en appuis vertical les jambes de force contre le plateau et je continue de lever jusqu'au ce que les "pinces" passent sous le plateau. Ensuite je rebaisse doucement pour que le plateau vienne en appuis sur les "pinces" qui supporteront l'essentiel de son poids. Je relâche la pression du bras de levier pour ne pas laisser le moteur inutilement en tension, mais je laisse tout de même ce dernier en contact appuyé contre le plateau pour avoir un niveau de sécurité supplémentaire.
A partir de ce moment et de ce moment seulement, on peut commencer à mettre les mains sous le plateau de la table de bridage pour nettoyer le bac collecteur ou je ne sais quoi d'autre. C'est l'astuce que j'ai trouvé pour manipuler le plateau simplement, seul et sans faire le tour 15 fois.
Photos supplémentaires
Bilan de l'opération
Il faut préciser que tout est une affaire de compromis. Le choix des matières premières (dans mon cas en grande partie de la récupération) et de l'épaisseur de la tôle sont déterminants pour le coût de la réalisation et tous les choix techniques qui devront-être faits en conséquence (choix des roues, puissance du moteur, résistance de chaque éléments, etc). Pour ma part, j'ai pris acte que le mieux est l’ennemi du bien, je n'ai pas un usage quotidien intensif de ce matériel déjà très bien pour une utilisation personnelle et il faut faire des choix rationnels.
Il faut également noter qu'au moment de la fabrication de cette table de bridage qui a déjà quelque temps, j'étais débutant dans le travail du métal, du moins pour des projets de cette envergure et que je n'avais pour la fabriquer qu'un outillage limité et un sol en béton pas droit, sans surface de référence.
Donc oui, il existe beaucoup mieux, beaucoup plus gros, beaucoup plus solide, beaucoup plus beau, beaucoup plus fonctionnel, découpé au laser, rectifié, nitruré et j'en passe mais c'est un autre monde et je n'en fait pas une utilisation industrielle. Globalement, je suis très satisfait de ma table de bridage #DIY def qui me fait gagner un temps précieux pour toutes mes réalisations en métal et je suis certain que beaucoup aimeraient déjà avoir quelque chose d'équivalent pour « bricoler ».
Elle me permet de brider très facilement et rapidement mes pièces dans toutes les positions (avec des accessoires) pour ne pas qu'elles déforment avec la chaleur, elle m'offre une surface plane et propre pour travailler, elle dispose de nombreux rangements très pratiques, de nombreuses prises électriques et supports d'outils, etc.
Bien entendu, elle n'est certainement pas à la hauteur d'une table de bridage haut de gamme du commerce, mais elle suffit à couvrir tous mes besoins et possède tout un tas de fonctionnalités sur mesure que l'on ne trouve pas sur les modèles manufacturés courants, ou alors à des prix stratosphériques.
L'essentiel n'est-il pas d'être satisfait de ses outils et qu'ils fassent ce pour quoi on les a conçus ?
Au rayon des regrets, je n'en ai qu'un seul, c'est une stupidité de ma part, j'ai installé le bouton de commande du moteur... du côté du moteur. Mais il est du mauvais côté, il aurait fallut le mettre en face, du côté où le plateau se soulève pour positionner les jambes de force. Ça m'aurait simplifié la vie mais le déplacer maintenant serait trop compliqué et chronophage pour le gain attendu. J'ai contourné ce souci mineur facilement, mais voilà ce que je ferais différemment.
Si je décide un jour de refaire son plateau s'il était trop abimé, j'installerai une tôle d'épaisseur 10 mm (20 mm serait trop lourd) de meilleure facture, mais j'avoue ne pas être pressé de refaire 160 trous à la perceuse magnétique, ça avait bien occupé mes soirées...
J'ai fait tout mon possible pour écrire cet article et j'espère qu'il vous a intéressé.
Si tel est le cas, je vous encourage à me laisser un commentaire et à suivre IronWood sur les réseaux sociaux.
#FollowMe sur les réseaux sociaux