Réalisation d'un support de router SLED (ou CNC) destiné à surfacer le bois, réalisé à partir de poutres en OSB pour disposer d'une surface parfaitement plane et économique. En outre, sous le support est installé un grand bac de récupération des copeaux produits en quantités importantes par ce type d'outils.
Sommaire de l'article (cliquez pour replier le sommaire)
Projet de départ
Lorsque j'ai commencé à m'intéresser à la menuiserie, j'avais le souhait de pouvoir travailler le bois massif sans devoir pour autant investir dans des machines stationnaires coûteuses dont j'ignorais si je pourrais les "rentabiliser" un jour. Or, sans machines stationnaires, à minima une raboteuse dégauchisseuse, il est très difficile de travailler à partir de plateaux de bois massifs et je me suis donc mis en quête d'une solution alternative qui soit efficace, pratique et fonctionnelle.
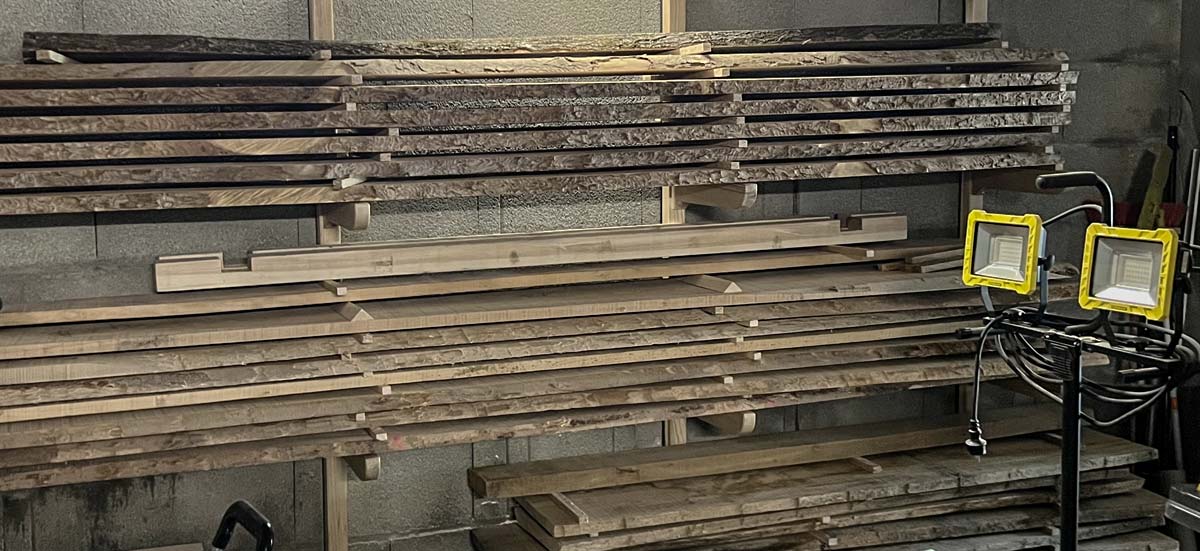
Je savais également que j'aurai des projets bois de taille importante (plans de travail, plateaux de tables, etc) et je voulais pouvoir traiter des pièces de relativement grandes dimensions. Une bonne dégauchisseuse fiable et précise (qui tienne ses réglages dans le temps) capable d'avaler des pièces de "seulement" 40 cm de large est déjà très onéreuse.
Certains me diront que je n'ai pas besoin de passer des pièces aussi larges, qu'un plateau s'assemble avec des collages de pièces préalablement dégauchies et rabotées beaucoup moins larges, car une réalisation faite à partir d'un plateau unique de grande taille travaillerait énormément, etc. Et ils auront parfaitement raison, c'est bien de cette façon que je procède en prenant soin d'établir les bois, sauf que…
Sauf que mon choix s'est porté sur une solution différente qui me permettra de traiter des grandes et des petites pièces sans trop perdre de temps par rapport à une configuration classique rabot/dégau, et qui me permettra aussi de rainurer et réaliser diverses opérations avec précision. Le tout pour un budget raisonnable toujours dans l'esprit Do It Yourself def, solution pensée pour être éventuellement motorisable et qui deviendrait le cas échéant une CNC.
Je voulais donc d'emblée fabriquer dès le départ un système suffisamment dimensionné et évolutif pour ne pas avoir à y revenir X fois à l'avenir, ce qui serait une pure perte de temps et d'argent. Le fait de pouvoir passer un plateau complet après collage (en cas de désafleurs par exemple), ou si je souhaite modifier son épaisseur a posteriori, ou encore si je souhaite pouvoir dégauchir un plateau complet avant de le déligner est très pratique. Il m'arrive de dégauchir un plateau complet avant de le déligner s'il n'est pas trop gauche (sinon la pertes d'épaisseur est trop importante sur des grandes dimensions) lorsque j'ai par exemple des doutes sur son état de surface après rabotage ou sur la façon de l'exploiter.
Pourquoi je vous parle de ça alors que cet article est dédié uniquement à la fabrication d'un support destiné à recevoir ensuite un router ? Tout simplement parce que la taille du support définit la taille du router et que les deux cahiers des charges sont indissociables. C'est donc par là que ma réflexion a commencé.
Le cahier des charges
Je souhaitais donc réaliser un support de grande dimension (pour recevoir un router ad hoc) avec pour objectif de réaliser un ensemble pertinent qui ne coûte pas trop cher. Sinon à quoi bon ? autant filer directement au "magasin de rabot/dégau" et faire briller le chéquier (sans oublier l'attente parfois longue liée au manque de disponibilité post-COVID de certaines références).
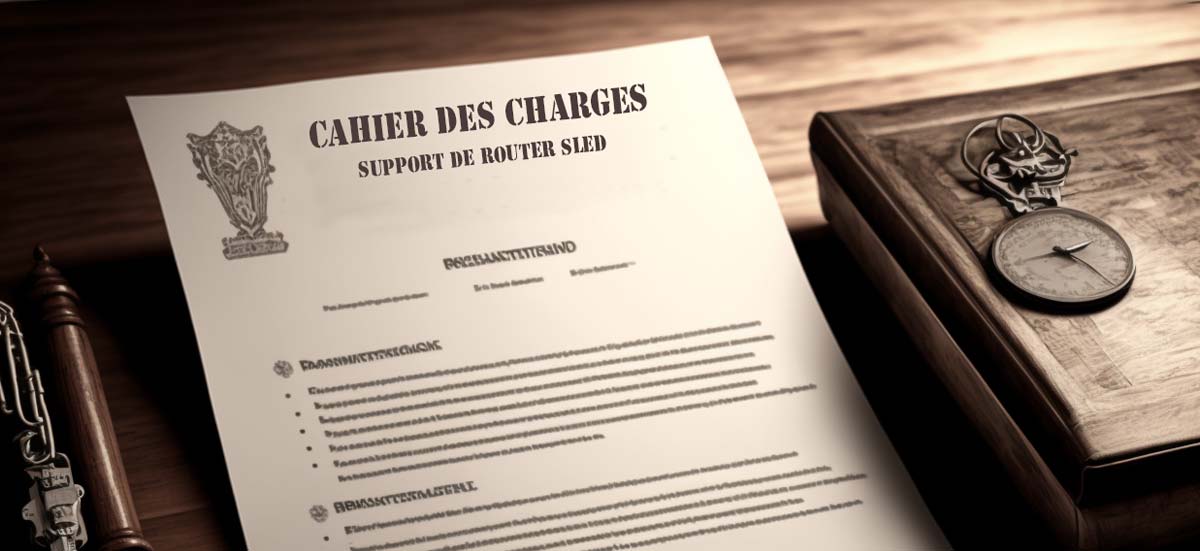
L'idéal serait bien entendu une bonne raboteuse dégauchisseuse complétée par une grande CNC mais ce n'est clairement plus le même budget et ce sont des configurations plutôt réservées à des professionnels ou à ceux qui ont gagné au loto. Si d'ailleurs ça devait m'arriver, ce n'est pas une rabot/dégau que j’achèterais mais une planche de surf avec une machine à cocktails et direction le meilleur menuisier d'Australie pour parler aménagement de ma villa dans la baie de Sydney 😎
Trêve d'humour car je ne joue pas au loto, 100% des perdants ayant tenté leur chance… Ça n'aurait donc aucun sens pour moi d'aller investir des fortunes dans un setup aussi onéreux, ce n'est pas mon activité professionnelle. J'ai donc réfléchi à trouver le meilleur compromis coût, capacité, efficacité et rapidité de mise en œuvre pour ne pas être freiné dans mes aspirations créatives et je pense l'avoir trouvé, en tout cas pour moi, ce qui pourrait ne pas convenir à d'autres.
Mon cahier des charges/contraintes était donc le suivant :
- Support pour recevoir un router capable de traiter des pièces de plus de 200 cm de longueur par 100 cm de largeur ;
- Étant donné la quantité de copeaux générés par ce type d'outils (il est difficile d'en aspirer la totalité en sortie de défonceuse), je souhaitais réaliser un support doté d'un grand bac de récupération pour ne pas en voir jusqu'aux genoux comme on le voit dans pas mal de vidéos ;
- Réalisation d'un support (puis d'un router) économique qui permette un investissement moindre que du matériel professionnel, tout en offrant peu ou prou les mêmes possibilités ;
- Comme ce fût l'un des premiers outils que j'ai créé, le challenge consistait à réaliser un support parfaitement d'équerre et plan alors que je ne disposait pas vraiment d'une surface de référence de taille suffisante pour le réaliser dans de bonnes conditions ;
- Que le support soit en bois (ou à base de bois), je ne souhaitais pas réaliser un cadre en acier pour cette machine ;
- Que le support reste partiellement démontable pour éventuellement sortir par la porte ;
- Monter le router sur roulettes pour pouvoir le déplacer rapidement, même avec un bac plein ;
- Arriver à une précision de ± 2 dixièmes de millimètres sur la totalité de la surface du router (et donc sur les futures pièces qui en sortiraient) ;
- Utiliser autant que faire se peut ce que j'avais déjà plus ou moins sous la main, en l’occurrence pas mal de plaques d'OSB de 14mm (bac collecteur) et 18mm (structure) dont je n'avais pas d'utilité immédiate (surtout les 14 mm dont je souhaitais me débarrasser qui sont passées dans ce support et une maisonnette à ossature bois isolée pour mon chat).
Voilà dans les grandes lignes mes contraintes et les objectifs que je m'étais fixés, passons maintenant à la réalisation.
La vidéo de la conception
Cet article complète une vidéo de la conception du support. Bon visionnage et n'oubliez pas de vous abonner à la chaîne si le contenu proposé par IronWood vous plaît 🙂
Réalisation du cadre du support
Comme je l'ai déjà indiqué, je ne souhaitais pas faire le cadre en acier mais à base de bois. Le bois massif est onéreux, il travaille dimensionnellement (même s'il bouge très peu dans le sens longitudinal) et ce support devait recevoir une structure aluminium. Je n'avais pas non plus trop envie d'utiliser du bois de palette pour baisser les coûts.
J'ai donc fait le choix de fabriquer des petites poutres en OSB à partir de collages, c'est rigide et ça ne bouge plus. Je possédais un outillage qui me permettait de faire des coupes précises et répétables sur des longueurs jusqu'à 280 cm, ainsi que des collages avec les mêmes qualités. Si tout est bien coupé et collé au départ et que l'assemblage n'est pas fait n'importe comment, en principe le résultat offrira une surface plane pour recevoir le router.
J'ai donc commencé par débiter des planches d'OSB de 10 cm de large pour les coller par 4 épaisseurs de 18 mm, ce qui m'a donc donné des poutres de 10 x 7,2 cm qui seront placées sur la tranche. Et il en a fallut un certain nombre avec pas mal de colle blanche, mais c'est relativement simple à mettre en œuvre.
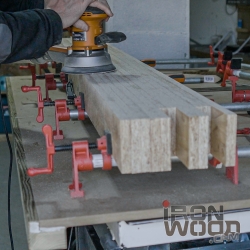
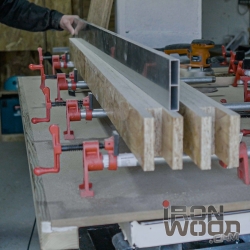
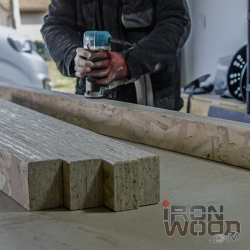
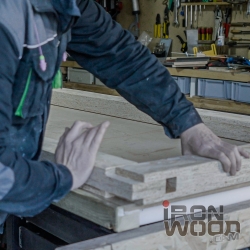
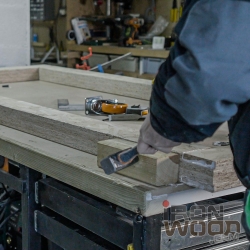
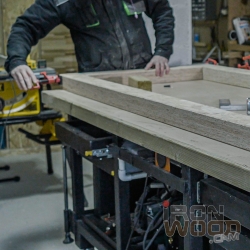
Il est également facile de prévoir les emboitures pour l'assemblage en coupant aux extrémités les 2 couches centrales ou externes plus courtes (emboitures mâles ou femelles). J'ai réalisé ainsi les traverses longitudinales et latérales hautes et basses ainsi que les pieds, ce qui a pris un certain temps. Pour aller plus vite, je collais les poutres par 3 ou 4 unités à la fois avec des grands serre-joints puissants.
Assemblage du cadre
Les traverses longitudinales hautes et basses ont été assemblées collées (emboitures) avec les montants verticaux aux extrémités, créant de grands rectangles solides et rigides. Les transversales ont été assemblées avec des équerres pour que l'ensemble reste démontable. La porte du futur atelier mesure 85 cm de largeur de passage et le routeur 140x213 cm. Comme il est fabriqué avec des traverses hautes et basses qui forment un gros parallélépipède rectangle, il ne serait pas possible de le passer sur la tranche. Il fallait donc anticiper le besoin de le sortir un jour pour un déménagement par exemple, ce serait dommage d'être obligé de tout casser.
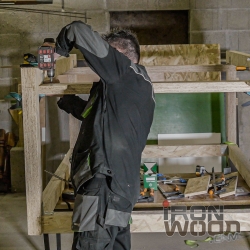
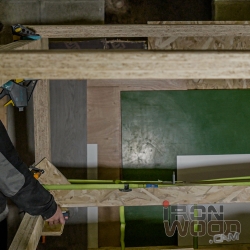
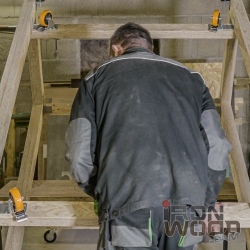
Même si je n'aime pas trop ça pour mes réalisations en bois (en même temps c'est de l'OSB 😎), j'ai donc été contraint d'utiliser des vis. Une fois le cadre assemblé, je n'avais pas prévu de montants verticaux de reprise de charge au milieu des traverses longitudinales car ça me semblait suffisamment rigide sur le papier.
Mais après vérification, j'avais tout de même un très léger jour lorsque je posais la règle dessus. J'ai donc été pris de remords en repensant à mon objectif de précision de 2/10ème et j'ai rajouté des montants. Comme je n'ai pas eu le courage de me relancer dans une séance de coupe et de collage de poutres OSB, d'autant plus que j'avais rangé tous les outils, j'ai donc cédé aux sirènes de la facilité. J'ai utilisé deux morceaux de traverses de palettes industrielles pour les caler en lieu et place. Et ça fait très bien le job, même si ce n'est pas "académique".
Il faut parfois savoir transiger avec ses principes si on ne veut pas y passer tout son temps ! Et justement, je voulais aller relativement vite. J'aurais pu fabriquer un superbe meuble en bois massif (encore que je n'avais pas de quoi raboter/dégauchir à ce moment), mais il me semble que ça n'avait aucun sens pour l'usage prévu.
Réalisation du bac de récupération des copeaux
Bon alors là ça se gâte, parce que mes panneaux d'OSB n'étaient pas assez large pour réaliser chaque paroi inclinée du bac en une seule pièce. Ce fût donc un peu galère et du bricolage au sens premier du terme avec des assemblages de planches plus ou moins heureux, mais ça fait le job.
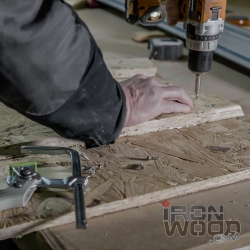
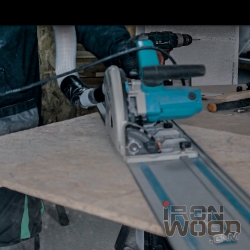
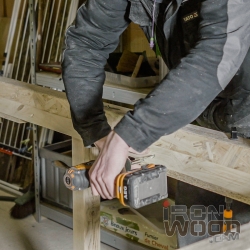
J'avais essayé pour la conception de définir les côtes de ces parois sur un plan Sketchup que j'avais fait pour le cadre mais à l'époque je ne maîtrisais pas très bien le logiciel et je n'arrivais à rien de satisfaisant avec les obliques, notamment pour les coupes.
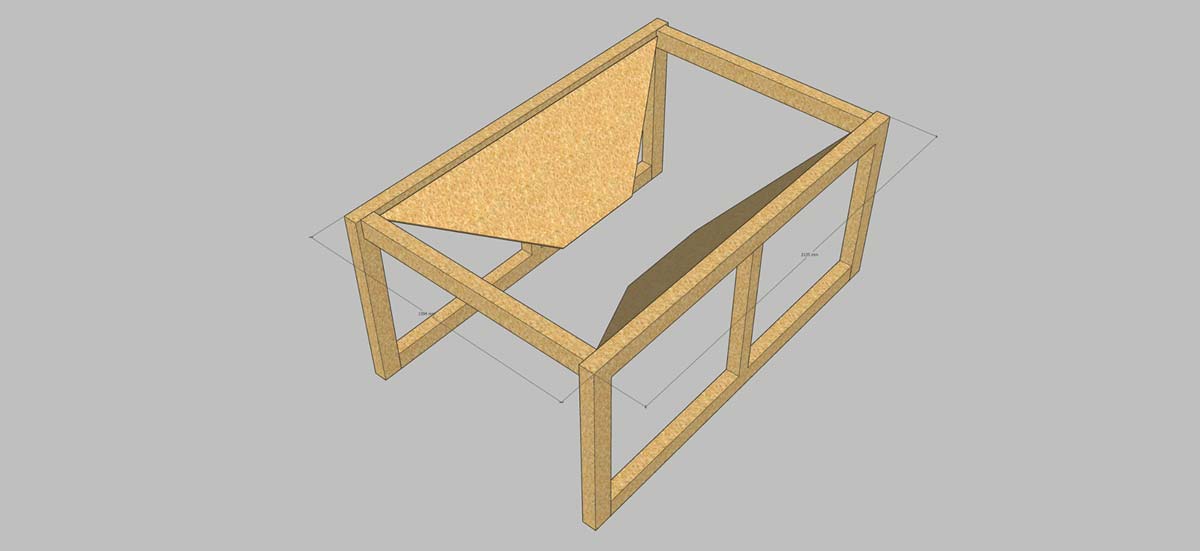
Comme pour la fabrication du bras de levier de ma table de bridage, j'ai donc invoqué les dieux de l'empirisme. J'ai procédé par tâtonnements en positionnant sur le cadre les parois longitudinales assemblées et coupées en fonction de la taille de la trappe à copeaux que je souhaitais. Je les ai calées par en dessous avec une traverse pour pouvoir les fixer et une fois satisfait du résultat, j'ai mesuré et reporté les cotes pour les parois manquantes aux extrémités.
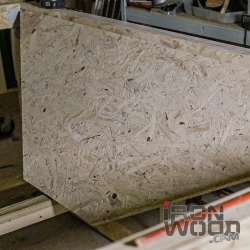
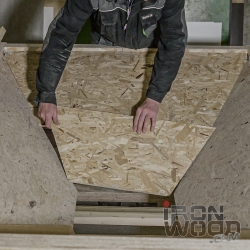
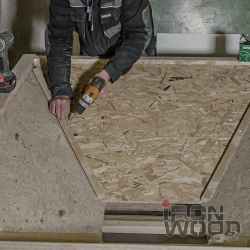
J'ai ensuite coupé les derniers panneaux (parois de la largeur du support) en trapèze avec un biseau au bon angle pour augmenter la surface de contact et limiter les interstices, avant de les mettre en place et les fixer pour fermer le cône du bac de récupération. Pour solidariser l'ensemble, je ne me suis pas trop cassé la tête, j'ai vissé dans chaque angle (aux jonctions de plaques) des tasseaux en pin biseautés. Je craignais que des vis uniquement à travers l'épaisseur des panneaux ne suffisent pas.
Pour la trappe, j'ai fait au plus simple, c'est une planche dans 2 glissières fixées sous le dessous, avec une tirette en bois pour pouvoir l'attraper facilement. Pas besoin d'avoir une super étanchéité, la sciure bouche très rapidement les interstices qui peuvent subsister et il n'y a quasiment jamais ou très peu de sciure sur le sol. Et finalement, je n'utilise pas la trappe car j'ai aussi vite fait de vider le bac avec une pelle que d'aller glisser un sac dessous. Mais elle existe en cas de besoin.
Vous avez sans doute remarqué que je n'ai pas perdu de temps avec certaines finitions, je n'avais pas envie de passer 2 jours à travailler sur des tasseaux en pin pour cette réalisation, ça n'avait aucun intérêt. La fabrication de cet équipement (conception, sourcing & approvisionnement, production) demande déjà énormément de temps et je préfère en perdre sur des optimisations (notamment du router) qui apporteront réellement une plus value. Ce n'est pas un meuble qui va trôner dans mon séjour et même si je prône l'amour du travail bien fait, parfois il ne faut pas être maso non plus 🙂
Le support de router terminé
Voilà, le support est prêt à recevoir son hôte, un router SLED qui va pouvoir cracher ses copeaux dans un grand bac de récupération, pour travailler proprement. Les dimensions du support achevé sont 213 cm de longueur, 140 cm de largeur et 91 cm de hauteur (sur roues).
J'envisageais de créer des rangements, notamment des tiroirs, en utilisant la place disponible sous le support le long des parois du bac de récupération, mais ça risque d'être assez long et fastidieux en raison des obliques. Finalement, j'hésite un poil à me lancer là-dedans, je pense que je vais me contenter de créer juste quelques petits rangements pratiques pour y laisser les principaux outils liés au router (un tournevis hexagonal, la clé du porte fraise de la défonceuse, un mètre, un crayon, les accessoires de la fraise de surfaçage comme les plaquettes de rechange, etc). Je verrai à l'usage si je trouve la motivation et surtout le temps de rentabiliser cette place.
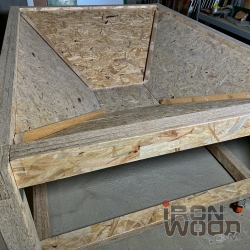
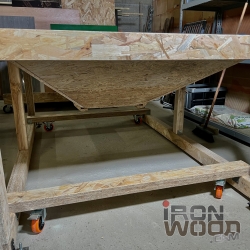
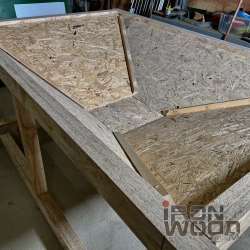
Je ne sais pas ce que vous en pensez, mais à mes yeux, ce type de réalisations purement utilitaires ne sont vraiment pas les plus intéressantes à réaliser, alors même que c'est ensuite parmi les plus utiles. Ce n'est pas franchement passionnant de couper et assembler des panneaux d'OSB et c'est relativement long à réaliser. Quand en plus ça nous oblige à manipuler des grandes pièces encombrantes et lourdes, c'est pénible mais il faut trouver la motivation et s'y coller, parce qu'ensuite c'est une vraie satisfaction de pouvoir bosser confortablement avec de bons outils. C'est d'autant plus satisfaisant quand vous les avez fabriqués.
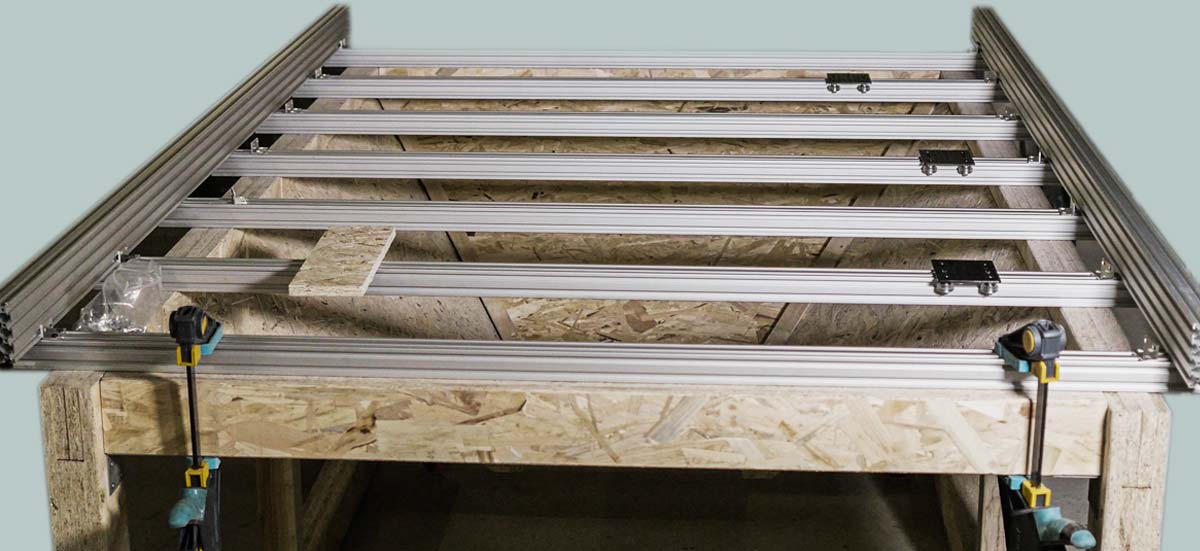
Quand j'ai conçu ce projet, au départ je ne savais pas vraiment où j'allais ni quelle serait la taille idéale. Nous pourrons reparler de la taille du router (qui avec le recul me convient parfaitement), mais pour ce qui concerne la taille du bac de récupération, il est largement assez grand et profond. Il permet de surfacer plusieurs grands plateaux recto/verso sans devoir le vider et je ne l'ai jamais rempli à plus des deux tiers. Du fait de sa forme évasée, plus il se remplit, plus il faut de copeaux pour que le niveau monte. Lorsqu'il arrive environ au niveau des 2/3 de sa contenance, je remplis pour le vider 2 grands sacs de 150 litres de copeaux bien tassés.
Sur la photo ci-dessus, vous voyez les premières étapes de l'assemblage du router, mais pour éviter que cet article ne devienne trop long, j'ai préféré écrire deux articles distincts, un pour le support, l'autre pour le router. Je vous invite donc à lire la suite, la réalisation du router SLED qui a trouvé sa place sur ce support pour le plus grand bonheur de son papa 😂
J'ai fait tout mon possible pour écrire cet article et j'espère qu'il vous a intéressé.
Si tel est le cas, je vous encourage à me laisser un commentaire et à suivre IronWood sur les réseaux sociaux.
#FollowMe sur les réseaux sociaux